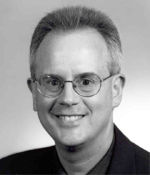
Scott E. Mackler
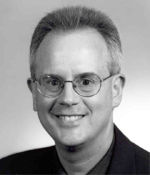
MBA degree from the University of Houston.
At Cleanroom Consulting, Mr. Mackler has led the basis of design (conceptual design phase) teams for projects in the life sciences (human blood products-based therapeutics and autologous cell transplant) and has acted as owner representative for a spinal nerve cell therapy center as well as being actively engaged in biotechnology projects for tissue culture applications and for the manufacture of therapeutic proteins via microbial expression systems and mammalian cell culture. Pharmaceutical clients include Schering Plough, Cambrex, Unigene, Merck, Sharpe & Dohme, and Guilford.
Mr. Mackler also authored a strategic marketing and product development plan (“stage/gate” process) for a revolutionary new enabling technology for ELISA (enzyme linked immunoassay) testing. Mr. Mackler has provided cleanroom compatibility testing and recommended actions to semiconductor inspection tool manufacturers. He has provided on-site consultation to cleanroom contractors performing work at DuPont (semiconductor wafer fab pilot project), Lucent (fiber optics cleanrooms) and at Balazs Labs (airborne molecular contamination laboratories) as well as for new nanofabrication facilities, precision cleaning and verification facilities, high bay assembly cleanrooms, aseptic processing suites, solid and oral dosage form manufacturing plants, and has authored Cleanroom User Requirements Specifications and Cleanroom Facility Functional Specifications for a major control systems provider. Mr. Mackler has also completed several cleanroom projects for Eastman Kodak Company and is a Certified Lean Six Sigma Green Belt.
Mr. Mackler also provides contamination control consultation, troubleshooting and environmental assessment – including recommended actions – to a number of biotechnology companies, medical device injection molders, photolithographic stent manufacturers, and to the world’s leading manufacturer of high tech filtration products in support of their “Clean Team” facilities initiatives. Mr. Mackler has been a member of the Licensing Executives Society and serves on the Editorial Advisory Boards of A2C2, the Journal of Contamination Control, American Pharmaceutical Outsourcing, the journal dedicated to pharmaceutical and biopharmaceutical contract manufacturing, as well as Pharmaceutical Formulation & Quality.
Related Representative Experience
- Alpha Therapeutics (Blood Testing Facility), Memphis, TN
A large number of individual release assays were required to be performed real-time. The facility was the first of its type for this company and for this process and was delivered as a design/build Class 1000 retrofit (suite type layout) to existing laboratory space. - Guilford Pharmaceuticals, Inc., Baltimore, MD.
Potent compound containment facility for clinical trials production of a chemotherapeutic agent. Directional laminar flow (Class 100), 100% once-thru air, and negative pressure containment were utilized to provide fully validatable aseptic containment. - Cambrex, Baltimore, MD
Maryland Bio Center: Designed and built two facilities (10,000SF, BL-2 and BL-3 labs for contract microbial and cell culture upsteam/downstream) incorporating unidirectional functional flows for segregation and separation. HVAC systems featured multiple independent units for each complete suite (upstream and downstream processing). Modular components were used for maximum flexibility; the cleanrooms were suitable for commercial scale microbial as well as mammalian cell production. Special attention was paid to ensuring that large pieces of process equipment, such as reactor processing trains, could be readily moved in or out of the various suites, and every suite was designed to accommodate additional, future contingent process support services. Each suite featured dedicated media preparation rooms, buffer preparation rooms, and clean cold rooms. - Collogenesis, Boston, MA
Clinical Trials facility for collagen production. Class 10,000 cGMP rooms (suite type layout) were designed to accommodate large numbers of Baker Class II Type A/B3 biosafety cabinets required for product manipulations. Protection of product was extremely critical as the nature of the clinical procedure precluded any opportunity to practice QC release testing prior to patient injection. - Merck, West Point, PA
Class 100, BL-1/2 LS – Designed and built retrofit fast track cGMP cell culture vaccine facility for production of chicken pox vaccine. Unidirectional functional flows and flexible multi-zone HVAC design, required for this commercial launch facility utilizing roboticized roller bottle technology. - Unigene Labs (Turnkey Calcitonin Production Facility), Boonton, NJ
Design and turnkey construction of facility for recombinant therapeutic production from process development through to commercial phase, including aseptic fill and finish. The facility design (suite style) was replicated overseas for sponsor partners. Class 10,000/Class 100. - Proneuron Biotechnologies, Inc., Denver, CO
Program management for 1,200 SF, Class 100/10,000 cGMP cell therapy center, BL-2
Professional Associations
o Rochester High Tech Business Council
o Rochester Engineering Society, Inc.
o Parenteral Drug Association
o ASHRAE
o International Society of Pharmaceutical Engineers
o International Society for Cell Therapy
o Semiconductor Equipment and Materials International
o Institute of Environmental Sciences and Technology
o US-Israel Biotechnology Council
o AVS Science & Technology Society
o New York Biotechnology Association
List of Publications:
Modular Design & Construction, Part I: Project Planning & Design, Part 2: Installation & Maintenance. BioPharm, September/October 1992
Clinical Production Facilities; Delivery, Design, Operating & Regulatory Considerations, with Stephen W. Fitzpatrick, Ph.D., Pharmaceutical Technology, September 1995
Current Issues in the Design of Production Facilities for Cell & Gene Therapy. Genetic Engineering News, June 1996
Project Planning & Basis of Design for cGMP Cleanrooms, Parts 1 & 2. A2C2, The Journal of Microcontamination Detection & Control, May/June 1998
The Surprising Advantages of Modular Cleanrooms, with Patrick Boyle, CPA. A2C2, The Journal of Microcontamination Detection & Control, November 1998
The Case for Design/Build Cleanroom Facilities Delivery. A2C2, The Journal of Microcontamination Detection & Control, November 1999
Barrier Isolation Technology: Facilities Update. Pharmaceutical Technology, February 2000
Barrier Isolation Technology Can Improve Life Sciences Cleanroom Applications. American Pharmaceutical Review, November 2002
Environmental Monitoring: A Product of your Environment, Pharmaceutical Formulation & Quality, June/July 2003
Environmental Monitoring: “Particle Counts are Easy”. BioProcess International, February 2004
Upgrading the Precision Cleaning Process, Process Cleaning Magazine, September / October 2009
“Basis Of Design For Life Science Cleanroom Facilities”, Engineered Systems Magazine, April 2010
“Point of View: Facilities Cleanliness Requirements”, Controlled Environments Magazine, June 2010
Click here to download pdf